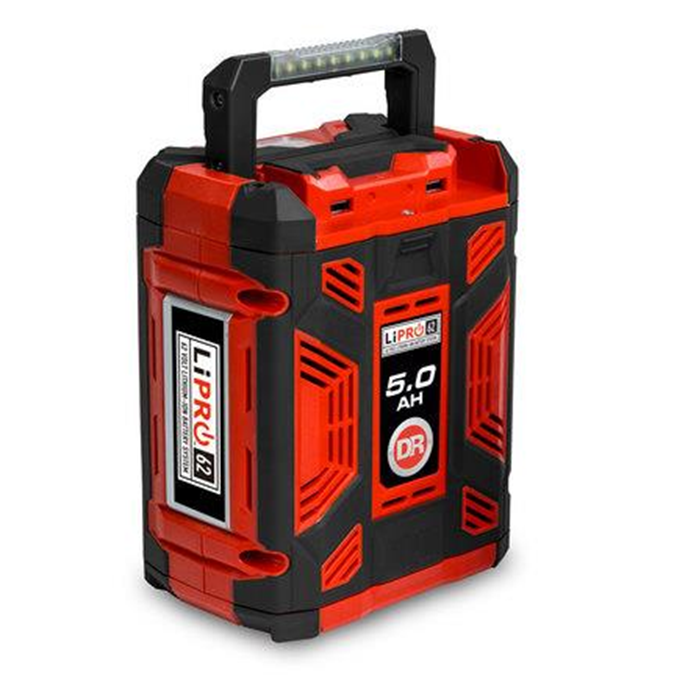
This article originally appeared in the CLM Magazine, a publication of the Claims & Litigation Management Alliance (CLM). Legal opinions may vary when based on subtle factual differences. All rights reserved.
It is once again that time of year when calendars are replaced and claims of freeze-induced sprinkler line failures exhaust any leftover holiday cheer. Although we may not see the historic low temperatures associated with the polar vortex of 2014, the winter season always brings with it an influx of freeze-related claims. Notably, the involvement of Mother Nature does not automatically preclude a subrogation recovery, and these types of claims should be triaged promptly and efficiently in order to avoid overlooking subrogation potential.
Freeze-induced sprinkler line failures occur when water inside a sprinkler system freezes. As this occurs, the water expands inside the line and can result in a fitting or a pipe cracking. In a wet line system, the water running through the line leaks into the building via the failure point. The same thing can even happen in a dry-line system, since a crack depressurizes the line and triggers the unnecessary flow of water. Regardless of the type of system, the result, inevitably, is a claim for water damage and the need to evaluate the potential for subrogation recovery.
As with other types of claims, it always is helpful to involve an expert as early as possible in the process. Although freeze-induced sprinkler failures typically are easy to identify, they sometimes can present in atypical fashions. Generally, a freeze-induced failure involves a broken pipe or failure in an area of a building that is subjected to cold temperatures. However, a freeze-induced failure also can present itself in heated areas.
For instance, if ice inside a sprinkler line is so thick that it completely blocks the line or creates what is referred to as an “ice plug,” the system can become over pressurized and cause a failure somewhere further down the line in a heated space. These types of freeze-induced failures are not always as easy to recognize. Additionally, the reported date of loss may be misleading. Sprinkler pipes may crack during the freezing temperatures, but the damage may not present itself until the first warm day after a cold stretch of weather because that is when the ice melts and allows water to leak. An experienced fire protection engineer will be able to identify freeze-induced failures and evaluate potential contributing factors other than the winter temperatures.
To assist with the cause investigation, the physical artifacts associated with the failure should be collected and preserved. This includes any pipe fitting fragments or other sprinkler components. The first responder to the site also should photographically document the valve room, pressure gauges, and inspection
tags for the sprinkler system prior to any repairs being made. Since sprinkler systems are considered life safety systems, most fire departments insist that the sprinkler system be put back into service as soon as possible. This does not always leave much time for a forensic examination. If possible, the portion of the line where the failure occurred should be isolated, capped, and left undisturbed while the rest of the system is put back into service. This will allow some additional time to inspect with the interested parties.
In addition to preserving the physical artifacts, some basic information should be gathered. For example, determine when the sprinkler system was installed and by whom. Find out if any work was done on or around the sprinkler system since it was installed. Ask the insured who performs service and maintenance for the sprinkler system, and make sure to differentiate between “service” and “maintenance.” Inspections and required testing may be performed by a vendor on a regular basis, but these tests typically do not include preventative maintenance. Thus, while most property owners contract for the performance of quarterly or annual tests referred to as “service,” there may not be a formal procedure in place for required “maintenance,” which might include the periodic draining of condensation from low points in a dry sprinkler system. To the extent outside vendors are involved, the contracts should be reviewed to ascertain the scope of the vendor’s work.
A thorough investigation of freeze related claims may identify failure modes involving human error that were simply brought to light by Mother Nature. For example, there may have been a failure to properly heat or insulate a sprinkler pipe during the original construction. In buildings that have been renovated, an addition or modification may have altered the flow of heat to an area that houses the sprinkler system, making the system more susceptible to freezes. Most jurisdictions have adopted the standards created by the National Fire Protection Association (NFPA) regarding the proper installation of sprinkler systems, including how to properly protect against freezes. The standards have changed slightly with the 2002 and 2013 revisions, but the benchmark for freeze protection continues to be 40 degrees Fahrenheit. In spaces that could be subject to temperatures below that number, additional steps must be taken to prevent freezing. This could include the installation of heaters in the attic spaces or physical padding placed around the pipes. Additionally, the NFPA standards provide the specifications for the proper slope of all pipes in a dry sprinkler system. Pipes that are not adequately sloped allow condensation to collect and freeze inside the line instead of draining to a dedicated low point. Construction not in compliance with the NFPA standards may support a claim alleging a design or construction defect despite the cold weather conditions.
Even if a sprinkler system appears to be designed and installed correctly, a subrogation claim still may be viable if the failure occurred on a dry sprinkler system that should not have contained any water. If a vendor fails to evacuate all the water following a full flow test, or if a property owner fails to drain condensation using the low point valves, there may be liability for creating a condition that allowed the freeze to occur. In these situations, “cold weather” is unlikely to be a valid defense.
When cold weather strikes, don’t assume Mother Nature is wholly to blame for freeze-induced sprinkler failures. Understanding the potential failure modes and key pieces of information will allow claims and subrogation professionals to quickly identify those cases with subrogation potential.
By Aaron Conrardy | Events, News
June 5, 2025